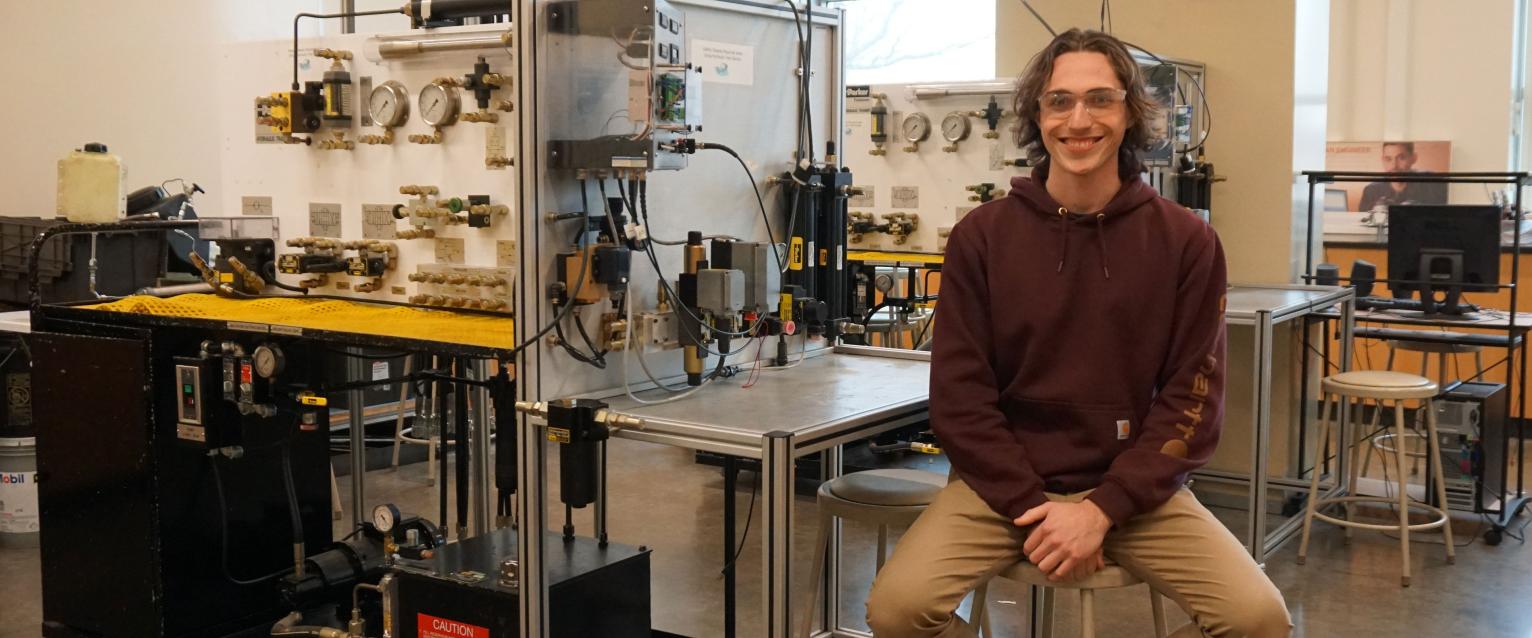
Motion and Control Laboratory
Supported through ongoing grants from Parker-Hannifin Corporation since 2003.
Th Parker-Hannifin Motion and Control Laboratory at Western Michigan University trains undergraduate and graduate engineers in hydraulic, pneumatic and electromechanical systems engineering. The lab is focused on hydraulic system engineering experiences and student exposure to pneumatic and electromechanical systems.